

This story…
…begins a couple years ago when I started the Omnicopter. To fly the copter, I needed a remote. So, I built the Omnimote (right). It was a Panda-II powered remote that used XBee to communicate with the copter. It also had a small (slow) FEZ Touch display that was useful for displaying some info but had limited ability as a touch screen due to it being a resistive touch screen and it was just too slow to be depended on for use during flight.
As I’ve built other projects since then, it’s become more and more evident that I have a need for a universal device that can communicate and display information with other projects.
In the past year, most of my focus has been drawn toward the Gadgeteer platform for electronics prototyping. It’s a much more flexible and productive platform than anything else that exists at the moment and has dozens of powerful modules (subcircuits) that can be attached to it. Gadgeteer has become my go-to platform when developing electronics projects.
I’ve been doing quite a bit of Gadgeteer evangelizing the past year by giving presentations at our local .NET users’ group and at conferences. I’m also starting the Nashville Microcontrollers users’ group. So, the desire to have a truly portable and compact solution for demoing Gadgeteer in addition to something that is useful for my other projects has become a little more important.
However, one piece has been missing to allow me to build the Gadgetab of my dreams – a large capacitive touch display. GHI Electronics recently solved that problem with the release of their CP7 module – a 7” capacitive touch display. So, let the building begin!
The design goal was to build a tablet type device that could be useful as a remote, demo device, have some room for storage, be battery powered, and look nice – lots of software & sawdust.
The Mounting Plate
It just happened that I’d been talking to Steve Presley, who is starting up a custom CNC & 3D printing service, about building some mounting boards for Gadgeteer projects. I gave him some dimensions and he went to work. A few days later, I received a perfectly CNC machined piece of 1/4” blue acrylic in the mail and I went to work building the box that would house it.
Constructing the Box
 | I started by taking a scrap piece of 3/4” walnut and cut it into three pieces. Two long pieces (9 3/4”) would serve as the top & bottom sides of the box. A 6” piece was cut for the other two sides of the box. |
The 6” piece was resawed using the table saw to produce two thinner pieces for the end sides of the box where the openings would exist. |  |
 | After resawing, the side pieces were ripped into two pieces to allow for the space on the sides where the external connectors would be located. |
Next, I used the router table to mill several dados in the pieces where they would fit together. |  |
 | Time for a test fit. Perfect fit! :) |
Let’s glue it up! |  |
 | While the sides were drying, I worked on the top & bottom. I found a wide piece of 7/8” walnut and cut it to 9 1/2” x 7”. |
I then resawed it on the bandsaw to produce two pieces roughly 3/8” thick. A quick pass on the thickness planer to smooth out the saw marks and ensure they were flat and they’re ready to go. |  |
 | After giving the glue 24 hrs to harden, I took the clamps off and glued up the top & bottom. Glue was brushed on to ensure 100% coverage of the glued surfaces. Too much glue is better than two little. The right amount of glue will produce some squeeze out that will help ensure you have no gaps. |
Using some scrap plywood as cauls to help ensure even pressure and to prevent the wood from clamp damage, I then clamped it up. Lots of pressure is essential here to ensure there’s no gaps and everything stays together. |  |
 | Wait another 24 hours then take off the clamps. Note all the extra glue on the box. Also, I forgot to wax my scrap plywood and it glued to the box along the edges. Not a problem… |
Using a hand plane and a card scraper, I removed the extra glue and plywood. Looking better, huh? |  |
 | Next, I put a 3/8” roundover bit in the router table and rounded over all the edges of the box to make it comfortable to hold in my hands. |
Using an orbital sander, I smoothed out any problem areas using 80 grit sandpaper then followed up with 120 grit sandpaper over the entire box. No reason to smooth it any further at this point. We’ll save the fine sanding for later. |  |
 | Time to cut a whole for the CP7 display. Since it’s hard to see pen marks on the dark walnut, I add some green tape to the areas to be cut and then mark out the opening for the display. |
Drill some holes in opposite corners big enough to fit a jigsaw into. |  |
 | Cut out the opening using a jigsaw then remove the tape. |
Time for a test fit. NICE! |  |
 | So, you’ve probably been asking yourself… “Self, how’s he going to open that box since it’s glued together?” Simple, we’re going to cut it in half. Fortunately, we only have to saw two sides of this box since the other two are already open in the middle. We line up the saw blade so that it cuts perfectly with the edge of the opening and set the blade height so that it’s just a hair short of cutting all the way though. We don’t want to cut all the way though or the box will flop around when we cut the other side and will create unwanted damage from the saw blade. Cut both sides. |
Using a hand saw, we’ll carefully cut out the hair thin piece that’s holding the two parts together. The box will likely pop apart shortly after you begin sawing. |  |
 | Clean up the remaining bits of the thin strip using a box cutter. |
Time for a test fit of the mounting plate. Oh yea! |  |
 | Those joysticks need holes now… |
Using a Forstner bit on the drill press, I make quick work of that task. | 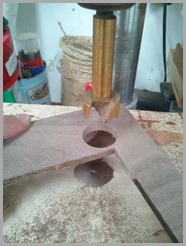 |
 | The joystick bases are semi-spherical and need a little more space. So, using a drum sander attachment on the Dremel tool we make the hole openings concave. |
Time to cut the dovetails… We start by routing a dado where the dovetail sliders will run. This will remove a lot of the wood and make the actual dovetail slot much easier for the dovetail bit and prevent it from breaking. We do this in two passes. Cutting half the height in each pass. We repeat these steps for all four dovetail slots (two on the top and two on the bottom) |  |
 | And finally, install the 1/2” dovetail bit and cut the slots. |
Lookin’ good? |  |
 | Now the tricky part… We have to cut the sliders so that they fit perfectly and don’t allow any slop and make the box appear lose. We cut some rectangular strips out of hickory (for color contrast) that are exactly the height from top to bottom of the slot and are exactly 1/2” wide. Keeping the dovetail bit at the same height, we adjust the fence so that it aligns over the bit such that the bottom corner of the bit lines up perfectly with the bottom edge of the hickory strip. Run each strip across the bit four times to cut the double dovetail slider. |
Test fit. SMOOTH! |  |
 | After sanding the entire box with 220 grit then some 400 grit sandpaper, it’s time to start applying the finish. I apply one heavy coat of Watco Danish Oil first and let it sit 24 hrs. Be sure not to leave any standing oil. |
After the first coat dries, I lightly sanded the whole thing in 400 grit sandpaper. Then I repeated this process with four coats of satin wipe-on polyurethane. Then I attached the CP7 using the double-stick tape that is supplied. AFTER the CP7 is mounted, apply a coat of paste wax to the box and polish it to a smooth sheen. |  |
This has been a fun project that yielded a platform that I’m sure you’ll see as an essential of many future projects. So, stay tuned and keep making!
Special Thanks
Steve Presley – for milling a perfectly fitting acrylic base plate. If you have any custom CNC or 3D printing needs, contact Steve.
Skewworks – for making the best UI controls available for .NET Micro Framework and letting me try out his new Tinkr controls.
GHI Electronics – for building the best Gadgeteer components and for setting the gold standard in customer support. They’ve also built the best NETMF/Gadgeteer community on the planet. Got Gadgeteer questions? Bring them to tinyclr.com.

Microsoft’s Channel 9 Coding 4 Fun site featured this project!
5 comments:
Hello,
Wow what a good job, I really like to case, esp the dovetail !
Steven (Gadgeteer team)
Thanks, Steven!
Good article. Sustain up the reliable performance.Thanks..........Router Mill
This is an excellent example of quality article content. It’s well-written, interesting, intelligible and uncomplicated. If I were a writer, this is how I would write this content. You have a lot of writing talent.
Router Mill
The stepper motors offer good torque and a higher corner speed than the similar 3Nm steppers.
CNC Routers
Post a Comment